5 Common Hydraulic System Failures and How to Avoid Them
Learn how to prevent common hydraulic system failures and keep your heavy machinery running smoothly. Discover tips for maintaining fluid cleanliness, preventing overheating, and inspecting seals and hoses. Protect your investment with these essential maintenance practices.
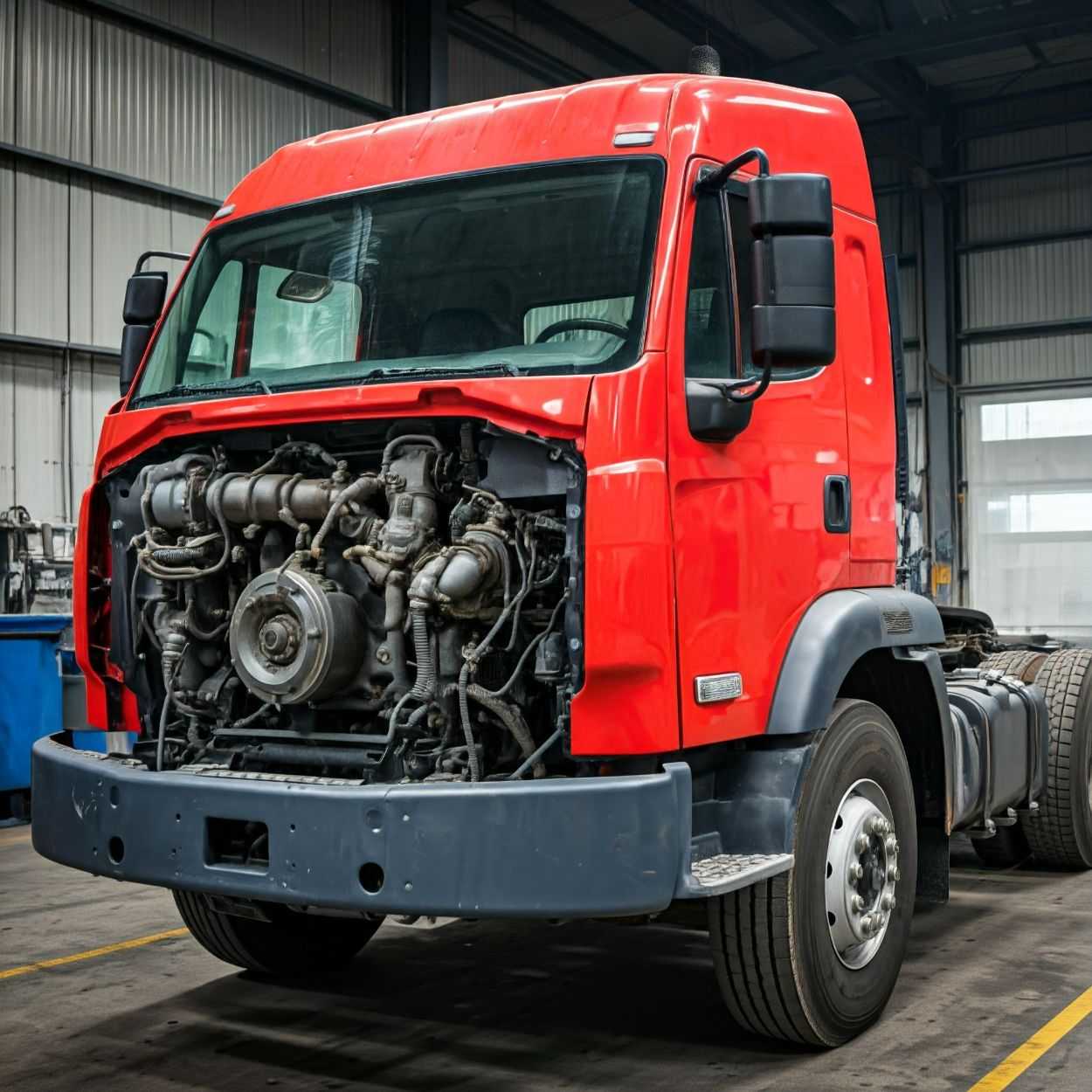
Hydraulic systems are the backbone of many heavy-duty vehicles, construction equipment, and machinery, enabling precise control and efficient power transfer. However, they’re also complex and prone to issues, especially if maintenance is neglected. Hydraulic system failures can lead to significant downtime, costly repairs, and potential safety hazards. Understanding the most common types of hydraulic system failures—and how to prevent them—can keep your machinery running smoothly and reduce unplanned breakdowns.
In this article, we’ll discuss five of the most common hydraulic failures and provide practical tips on how to avoid them.
- Hydraulic Fluid Contamination
One of the most frequent causes of hydraulic system issues is fluid contamination. Hydraulic fluid contamination occurs when dirt, metal particles, water, or other contaminants enter the hydraulic system. These foreign materials interfere with the fluid’s ability to lubricate and cool, causing wear on components like pumps, valves, and actuators.
How to Prevent Hydraulic Fluid Contamination:
- Use Proper Filters: Install high-quality filters and replace them regularly to capture particles before they reach sensitive components.
- Keep Reservoirs Sealed: Ensuring that reservoirs are tightly sealed can prevent contaminants from entering the system.
- Regular Fluid Testing: Perform regular fluid analysis to detect contaminants early. This can help identify contamination issues before they lead to severe damage.
By maintaining clean hydraulic fluid, you protect the entire system from premature wear and ensure optimal performance.
- Overheating of Hydraulic System Components
Hydraulic systems generate heat during operation, and excessive heat can lead to overheating of components, resulting in fluid breakdown, seal damage, and even permanent component failure. Overheating is typically caused by high workloads, low fluid levels, or blocked cooling systems.
Preventive Measures for Overheating:
- Monitor Fluid Levels: Low hydraulic fluid levels reduce the system’s cooling efficiency, so keep fluid at optimal levels.
- Inspect the Cooling System: Check cooling fans, radiators, and fluid coolers for clogs, damage, or wear.
- Use the Right Fluid: Use hydraulic fluid with the correct viscosity for your operating conditions. High-viscosity fluids can struggle to circulate and cool effectively, especially in hot environments.
Avoiding overheating helps to prolong the life of hydraulic components and maintain consistent system performance.
2. Air and Water Contamination in Hydraulic Fluid
Air and water contamination are two of the most common types of hydraulic fluid contamination, each with unique issues. Air contamination causes foaming and reduces the fluid’s ability to transmit pressure, leading to erratic operation and increased wear. Water contamination, on the other hand, reduces lubrication properties, causing rust and corrosion.
How to Prevent Air and Water Contamination:
- Bleed Air from the System: After maintenance or fluid changes, ensure all air is bled from the system to prevent foaming and erratic operation.
- Use Water-Absorbing Filters: These filters can capture and remove water from hydraulic fluid.
- Check for Leaks: Regularly inspect seals, hoses, and fittings for signs of leaks that could allow water or air to enter the system.
Maintaining clean, dry hydraulic fluid can significantly reduce the risk of contamination-related failures and improve the longevity of your hydraulic system.
4. Hydraulic Seal Failure
Seals are essential for maintaining pressure within a hydraulic system and preventing leaks. However, they’re also vulnerable to wear, aging, and damage from contaminants or improper installation. A failed seal can cause hydraulic fluid leaks, pressure drops, and decreased system efficiency.
How to Prevent Seal Failure:
- Choose High-Quality Seals: Invest in durable seals designed for high-pressure applications to reduce the chance of premature failure.
- Inspect Seals Regularly: Look for signs of wear, cracking, or damage during routine maintenance. Replace seals showing any signs of degradation.
- Avoid Over-Pressurizing: Excessive pressure can cause seals to fail prematurely. Make sure system settings match the seal’s pressure rating.
With regular inspections and proper installation, you can prevent most hydraulic seal issues and avoid pressure drops that disrupt system operation.
5. Hose and Fitting Failures
Hoses and fittings are critical for maintaining fluid flow and pressure within the hydraulic system, but they are also susceptible to wear and failure, especially in demanding environments. Common causes of hose and fitting failure include aging, abrasion, incorrect installation, and exposure to extreme temperatures.
Preventing Hose and Fitting Failures:
- Inspect Hoses and Fittings Regularly: Look for signs of wear, cracks, or leaks during routine maintenance.
- Use the Right Hose and Fittings: Ensure that hoses and fittings match the system’s specifications for pressure, temperature, and fluid type.
- Avoid Sharp Bends: Sharp bends in hoses can lead to kinking and increased wear. Use hose clamps or guides to prevent sharp angles.
Replacing worn hoses and fittings before they fail can prevent costly downtime and ensure smooth hydraulic operation.
Implementing a Preventive Maintenance Program for Hydraulic Systems
A proactive preventive maintenance program is essential to reduce the risk of hydraulic system failures. Routine maintenance tasks, such as regular inspections, fluid changes, and component replacements, keep the system in top condition and help identify potential problems before they become serious.
Key Components of a Preventive Maintenance Program:
- Scheduled Fluid Changes: Regularly changing hydraulic fluid prevents contamination buildup and keeps the system running smoothly.
- Routine Component Inspections: Inspect all components, including pumps, filters, hoses, and seals, to identify and replace worn parts before failure.
- Training for Operators: Training operators on proper hydraulic system use and basic troubleshooting can help prevent many avoidable failures.
A well-structured preventive maintenance program not only prevents unexpected breakdowns but also extends the life of your hydraulic system, saving on repair costs and maximizing uptime.
Importance of Using the Right Hydraulic Fluid
The type of hydraulic fluid you use plays a significant role in system performance and longevity. Using the wrong type of fluid can lead to overheating, poor lubrication, and other issues that accelerate wear on system components.
Selecting the Right Hydraulic Fluid:
- Check Manufacturer Recommendations: Always follow the manufacturer’s guidelines for fluid type, as each system has unique requirements.
- Consider Viscosity and Temperature Range: Choose a fluid with a viscosity that matches the operating temperature of your system for optimal performance.
- Use Additives as Needed: Some fluids come with additives that enhance their properties, such as anti-wear, anti-foaming, and rust inhibitors. Ensure your fluid has the right additives for your application.
Choosing the right hydraulic fluid ensures the system operates smoothly and efficiently, reducing wear and preventing many common failures.
Signs of Hydraulic System Failure to Watch Out For
Early detection is key to preventing complete hydraulic failure. Recognizing the warning signs of hydraulic issues can help you address problems before they lead to costly repairs.
Warning Signs of Hydraulic System Issues:
- Unusual Noises: Squealing, knocking, or rattling noises may indicate air contamination or mechanical issues.
- Slow or Erratic Movement: Reduced responsiveness in hydraulic functions can suggest low fluid levels, contamination, or internal wear.
- Leaking Fluid: Visible leaks around seals, hoses, or fittings should be addressed immediately, as they signal potential component failure.
- Overheating: If the system frequently overheats, check for low fluid levels, clogged filters, or faulty cooling systems.
Acting on these signs early can prevent minor issues from becoming major repairs and help maintain hydraulic system efficiency.
Conclusion
Hydraulic system failures are costly and can disrupt productivity, but many of these issues are preventable with regular maintenance and proactive care. By focusing on common failure points—such as fluid contamination, overheating, and worn seals—you can protect your hydraulic system and ensure it runs smoothly.
From keeping hydraulic fluid clean to using the correct hoses and fittings, these preventive measures go a long way in maximizing system reliability. A well-maintained hydraulic system enhances vehicle performance, reduces downtime, and ultimately saves on repair costs, making it an essential part of any maintenance program for heavy-duty equipment.
More Articles
Contact Us
Need roadside assistance, have questions, or want to schedule your truck or trailer in for a service or repair? Get in touch, we're open Monday through Friday from 6:00am to 5:00pm and on Saturday by appointment only.